Procedures & tools for controlled bolting:
The consequences of deviation must be understood
Aug 18, 2023

Imagine a scenario in which you receive a bill from your supplier and it contains their best guess for supply. How comfortable would you feel receiving this?
How about when you follow a recipe for a special meal but there are no metrics to measure the ingredients, no reference to equipment or even the temperatures to cook at? This information is essential if you aim for success with the dish. Should even one element vary from the required parameters, this special meal will go from not what I expected to potentially a very bad outcome.
Controlled Bolting Recipe
Controlled bolting activities such as flange assembly and tightening are essentially a recipe. This system of components provides facilities with assurance when maintaining process containment. In summary, the components for success can made up of the following:
Design (flange geometry, bolting quantity)
Process (procedures, forms, guidance cards)
Competency (technician training, competency to process)
Technological (gasket sealing performance, lubricant coefficient)
Equipment (method, number of tools to be used, calibration)
Broadly speaking there are two main categories of controlled tightening methods:
1. Torque
Within torque equipment there are 2 classifications; manual and powered (pneumatic, electric or hydraulic.) Torque uses applied force to rotate a nut.
2. Tension
Tension uses a temporary axial load applied directly to the stud thread form and is contained by the nuts fitted. All tension equipment is hydraulic therefore, powered.
Understanding Equipment
Understanding equipment capability is paramount to the success of a controlled bolting activity. There are a range of factors that need to be considered prior to selecting equipment that influence this choice. This potentially limits the method in which the bolt load is delivered or even the permissible final bolt load value. Complexity increases when powered equipment such as a hydraulic torque wrench is selected due to cases where minimum torque thresholds are stipulated by manufacturers.
Importance of Calibrated Equipment
For equipment to be considered for controlled tightening, it must be calibrated and capable of setting or measuring to a desired value on a readable scale, gauge or readout. Manual equipment comes in two broad categories: indicating and setting torque tools. Indication tools are read by the user to the correct value from exerted torque and setting torque tools. These are limited or indicate the reaching of a desired torque value by means of audible, visual or physical feedback. Powered equipment using hydraulic transmission will require a pump gauge, which in turn, requires it to be readable and calibrated.
Use of equipment that is uncalibrated can result in an outcome value being acutely set, however the actual output of the tool can experience drift or variation. Each and every time that a tool in this condition is used, it can be regarded as a gamble.
A game of chance to secure a critical component in the recipe of controlled bolting can also lead to; “not what I expected” and potentially a very bad outcome with greater consequences than a spoiled meal.
For further reading on calibration, please see:
ASME PCC-1 (2022) Pressure Boundary Bolted Flange Joint Assembly
ISO 6789-2
VDI 2646 – Torque measuring devices, minimum requirements in calibration
SHARE THIS
Do you have any questions?
If you have any questions, feel free to contact us at any time.
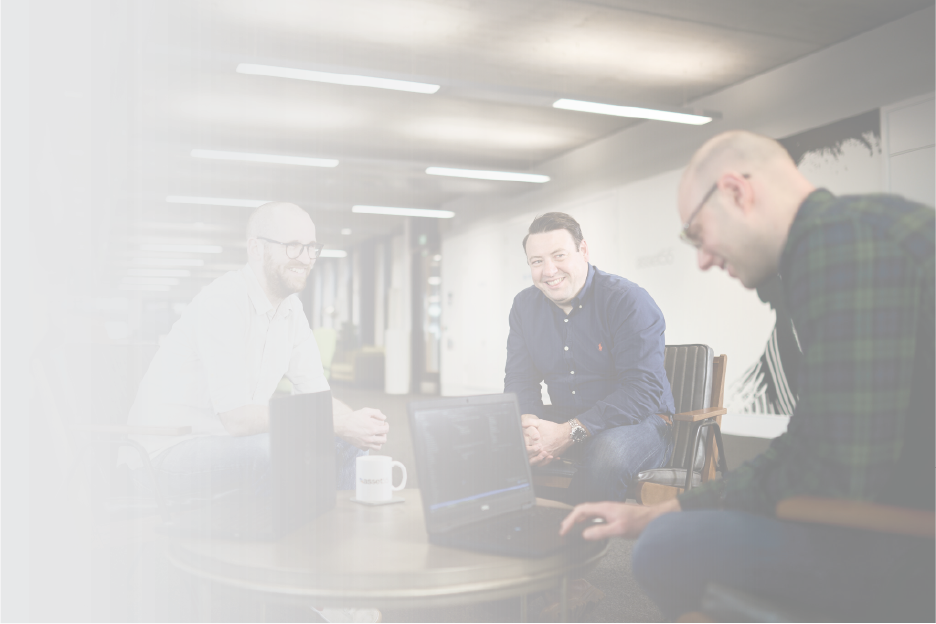